Description
Pad printing, also called tampography, is an indirect offset printing process that uses a silicone pad to transfer a two-dimensional image from a laser-engraved printing plate to a three-dimensional object.
Conventional printing processes cannot match the capabilities of pad printing, which is compatible with products with compound angles and spherical, cylindrical, concave, or convex shapes. This versatile process is used for many applications across industries.
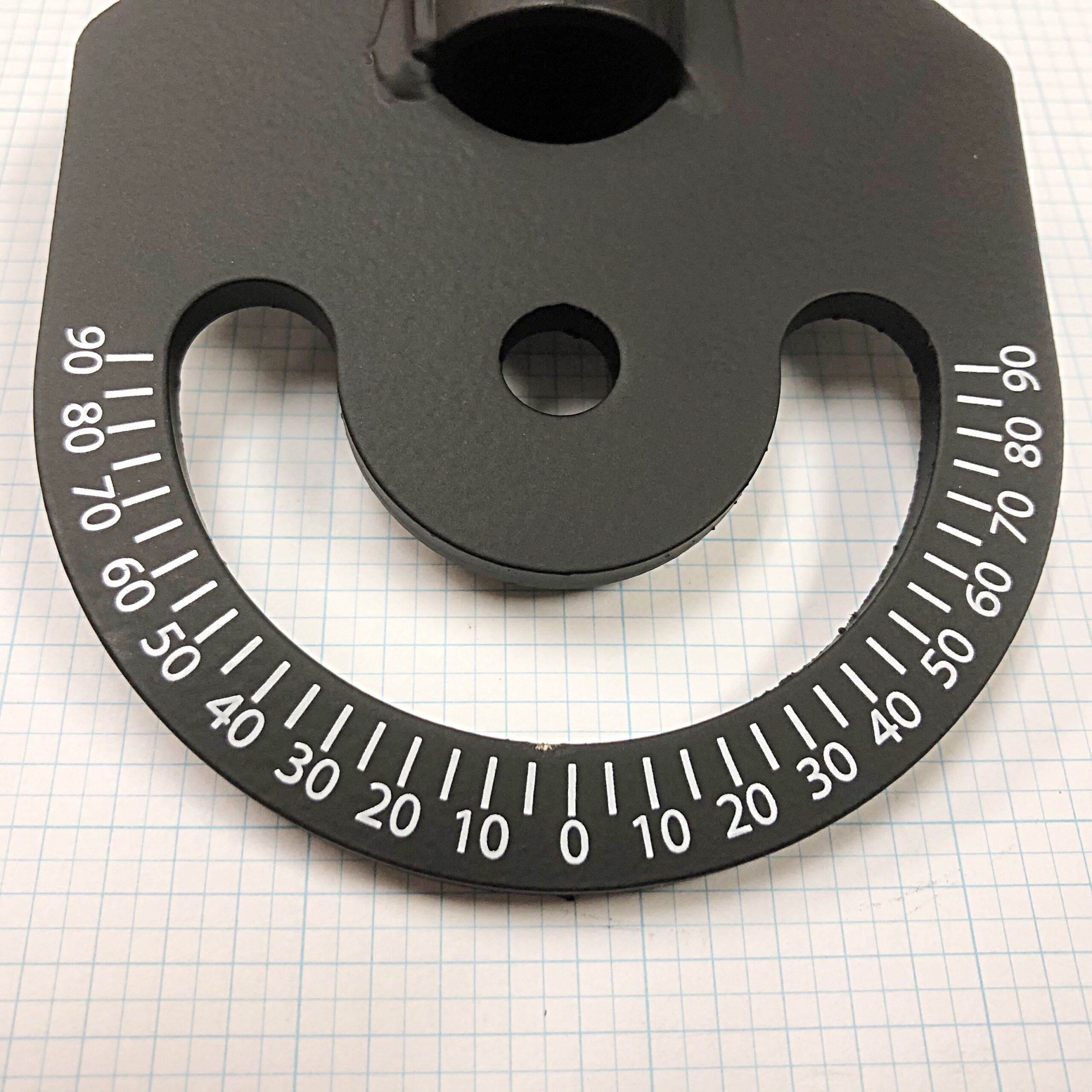
Pad Printing Process
Pad printing creates durable, clear, and eye-catching images and markings efficiently. These are the steps in each printing cycle:
- Step 1. The sealed ink cup sits over the etched artwork on the pad printing plate (i.e., “home” position) and fills it with ink.
- Step 2. The cup removes all of the excess ink from the engraved artwork area and moves away to expose the image. As soon as the top layer of ink is exposed to air, it becomes tacky and adheres to the transfer pad.
- Step 3. The transfer pad is pressed on the printing plate for a brief interval. This pushes out air and lifts the ink from the engraving and onto the printing pad.
- Step 4. A small amount of the ink film in the engraved area is picked up as the transfer pad lifts away.
- Step 5. The ink cup returns to the home position and refills the engraving with ink in preparation for the next cycle.
- Step 6. The transfer pad compresses onto the product and transfers the ink to it. The pad then lifts off the item cleanly and returns to the home position.
Pad Printing Benefits and Applications
Pad printing is compatible with many materials and types of products, including appliances, tools, parts, and consumer products. There are many reasons to use pad printing for adding logos, graphics, and printed markings to products, including:
- Material compatibility. Pad printing inks can be used with many materials, including rubber, ceramics, glass, metals, plastic, and wood, for a wide range of applications.
- Cost-Effective for Medium to High-Volume Production Runs. Pad printing balances cost and quality, providing an economical and efficient choice for medium to high-volume production runs.
- Extreme Accuracy and Fine Detail Capability. Pad printing reliably reproduces detailed logos, small fonts, and intricate designs. It is also used for high-resolution printing for applications with narrow line widths and small writing, such as electronic components and medical devices.
- Ideal for Textured, Curved, and Irregular Surfaces. The flexible nature of the silicone pad means this process can be used on textured, concave, and convex surfaces, making it suitable for applications in which traditional printing methods fail.
- Multicolor Printing Capabilities. Pad printing can apply multiple color layers with accuracy and precision for informational labels and decorative branding alike.
- Strong Ink Adhesion with Optional Post-Curing. Pad printing ink is durable and adheres well to many surfaces. It can also be specially formulated to resist abrasion, heat, and chemicals, depending upon the specific application.
Applications
Uses for pad printing are almost limitless. It can be used for labeling tools with instructions, warnings, or markings, for branding and marketing on promotional items, for adding logos or graphics to equipment, and more. Some common applications include:
- Automotive Parts and Components. Pad printing accurately prints finely detailed symbols and other marks on contoured or textured surfaces to communicate critical information. Durable inks remain intact, readable, and resistant to wear over time. Examples include traceability markings like labels and barcodes, symbols, and text on buttons, control knobs, and dashboards.
- Consumer Electronics. Pad printing can be used for marking clear, long-lasting metal and plastic components in electronics products. The method can effectively create logos, functional symbols, and branding features on headphones, GPS devices, laptops, smartphones, and other devices.
- Industrial Equipment. Industrial tools and heavy-duty equipment require safety warnings, in-site operating instructions, and legible serial numbers. Pad printing ensures these markings remain visible in harsh environments and exposure to grease, oil, chemicals, and extreme temperature fluctuations. Durable traceability markings help guarantee regulatory compliance, inventory management, and effective routine maintenance procedures.
- Injection-Molded and 3D-Printed Parts. As rapid prototyping and customization become prevalent in many industries, manufacturers need ways to mark injection-molded and 3D-printed parts. Pad printing allows labeling, branding, or instructional text to be applied accurately, even on non-uniform, irregular, or complex shapes and surfaces.
- Medical Devices. Pad printing is essential for marking surgical tools, instruments, and syringes with dosage instructions, traceability marks, and measurement indicators. The method ensures durable, legible markings on small or curved surfaces and holds up to repeated use and sterilization.
Pad Printing Services from Universal Marking Inc.
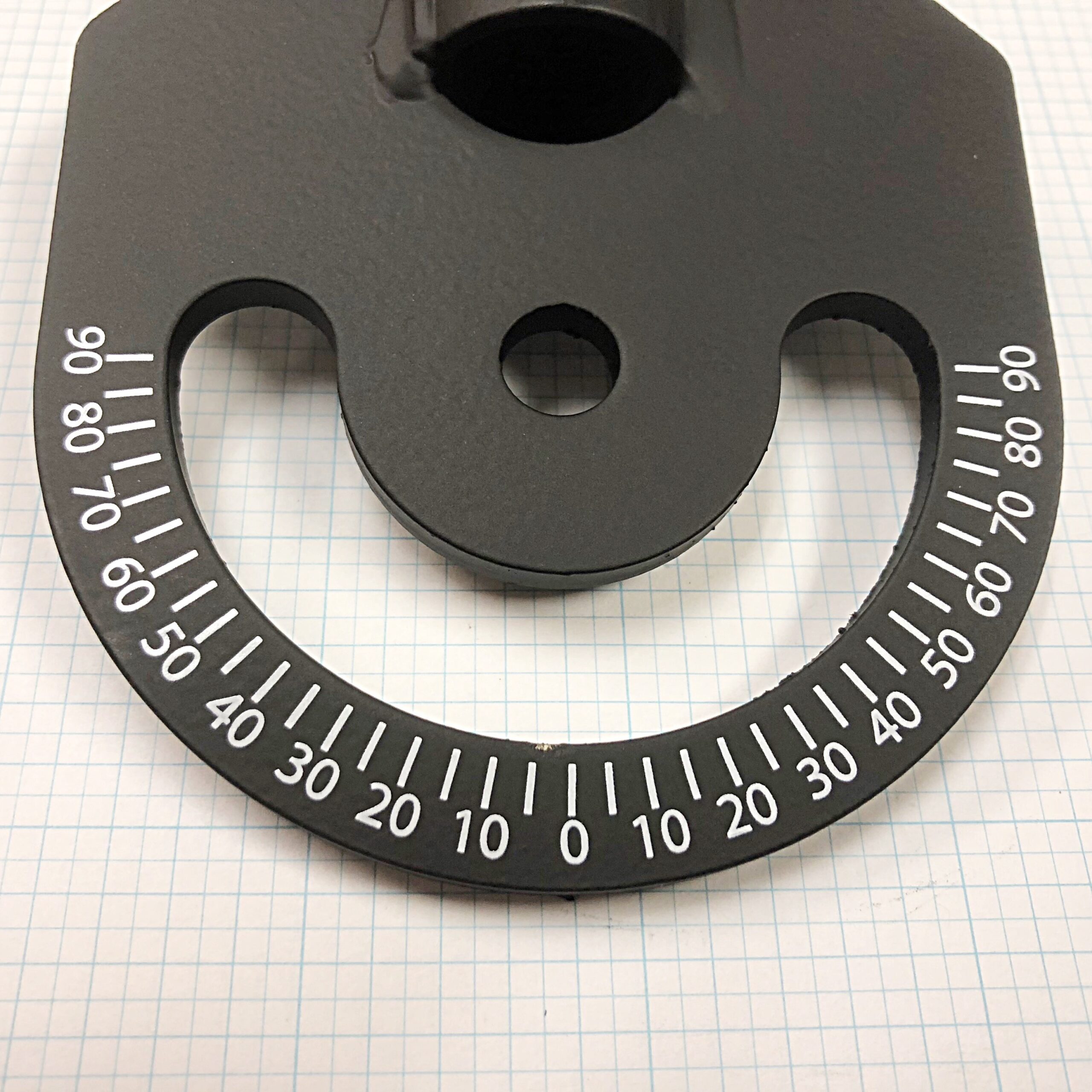
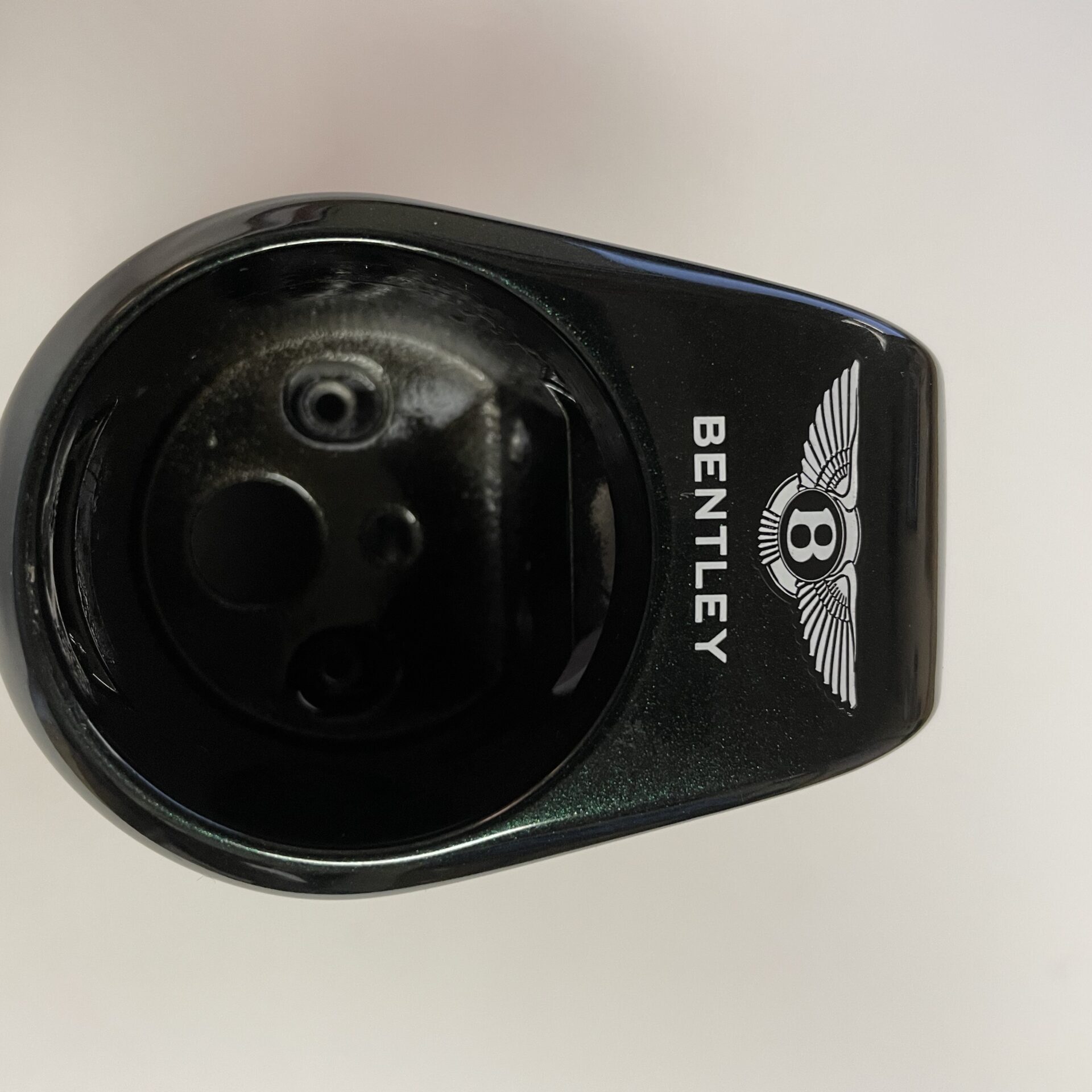
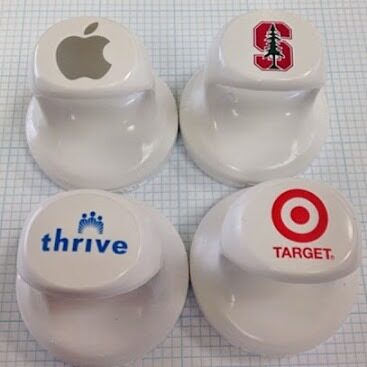
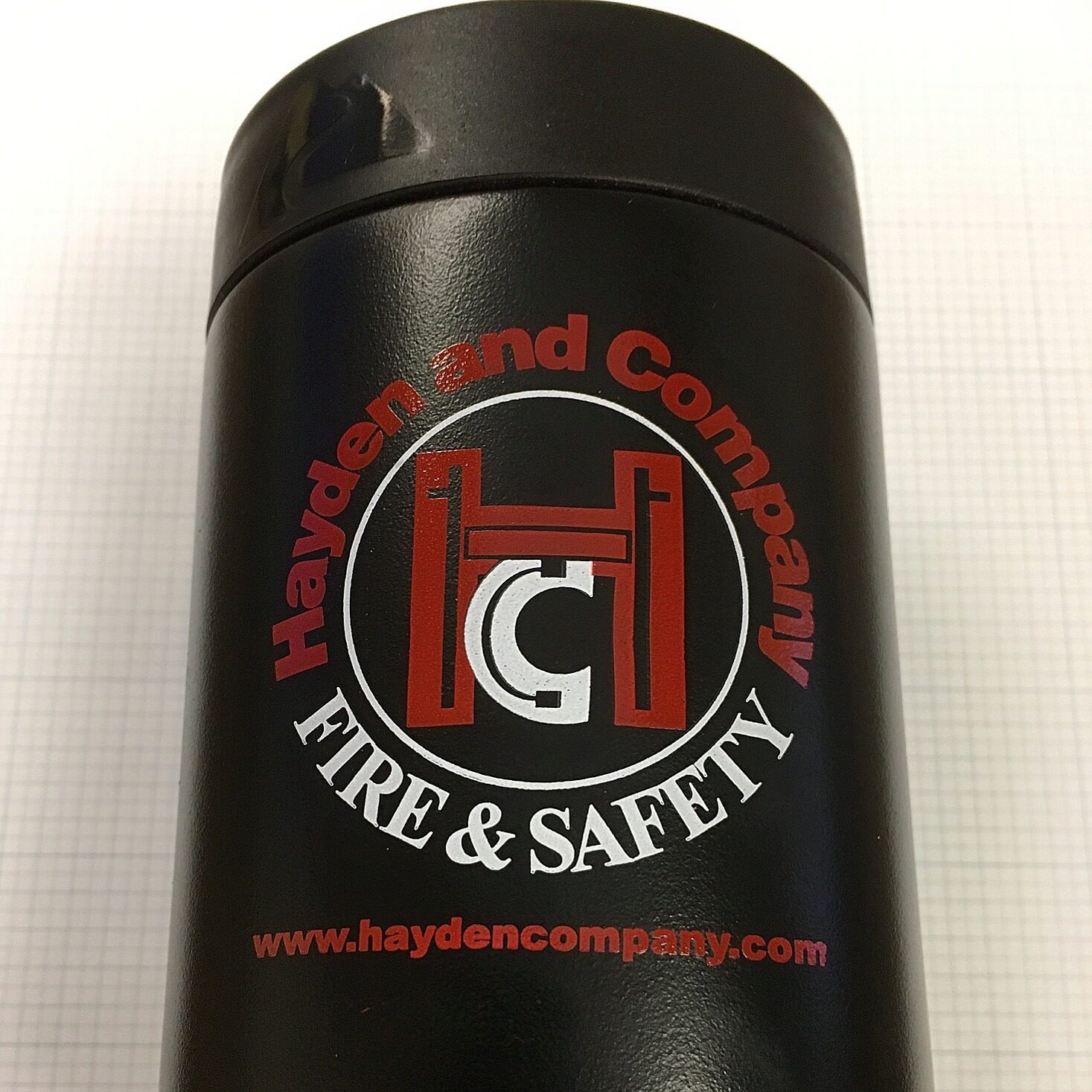
At Universal Marking Inc., we offer pad printing services for creating durable, clear markings and images for large and small production runs, and a large selection of color choices to complement products and parts. Our capabilities also include laser marking, engraving, electro-chemical etching, sand blasting, metal impression stamping, silk screening, and custom die making.
Contact us to learn more about our services or request a quote for your next printing project today.
Call (562) 634-6300 | Toll-Free (800) 803-8333 | Fax (562) 633-0600 | 14053 Orange Ave. Paramount, CA 90723
Monday - Friday 7:00 a.m. - 4:00 p.m.