A laser engraving machine uses a high-powered laser beam to precisely etch designs or text onto various surfaces, including metal, wood, plastic and glass. It employs a computer-controlled process to guide the laser beam, allowing for intricate and accurate engraving. Due to its ability to produce detailed and durable markings, it is commonly used in the manufacturing, jewelry-making, and signage production industries.
Universal Metal Marking Co. offers comprehensive marking and engraving services tailored to our clients’ needs. Our state-of-the-art facilities have advanced laser and traditional engraving technologies for various materials and applications. From small- to large-scale projects, we provide efficient and cost-effective solutions to fulfill different marking and engraving requirements.
How Laser-Powered Engraving Machines Work
Laser engraving machines employ modern technology to etch accurate drawings onto surfaces. These devices are driven by a high-powered laser source, which is commonly CO2, fiber, or diode lasers. The laser beam is managed by a sophisticated control system that analyzes digital designs and precisely controls the laser head’s motions.
When the laser beam reaches the surface, it reacts with the substance, resulting in localized heating and vaporization. This procedure — known as ablation — eliminates microscopic quantities of material to create the desired engraving. The focusing optics within the machine ensure that the beam is concentrated to a fine point, which results in sharp and well-defined markings.
A laser engraving machine typically has various safety features, including interlocks, emergency stop buttons, and protective enclosures. These features ensure the operator’s well-being and compliance with safety regulations. Additionally, exhaust systems eliminate debris and fumes generated during engraving, maintaining a clean and safe work environment.
Factors Influencing Engraving Quality
Considering and optimizing the following factors can help operators achieve superior engraving quality
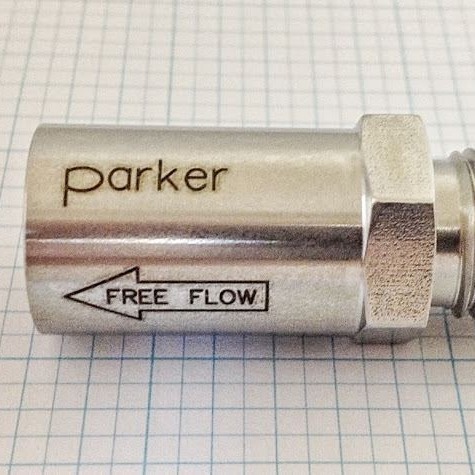
Laser Power
The power output of the laser source is a fundamental factor influencing engraving quality. Higher laser power enables deeper and faster engraving, particularly on tougher metals. On the other hand, lower laser power settings may be ideal for intricate designs or finer details to avoid excessive removal or heat generation.

Material Type and Composition
Materials vary in conductivity, reflectivity, and hardness, which affect how they interact with the laser beam. For example, highly reflective metals like copper or brass may necessitate higher laser power settings to overcome reflectivity and achieve satisfactory engraving depth. Meanwhile, stainless steel, titanium, and other metals with lower reflectivity may require lower laser power settings to avoid heat buildup.

Laser Beam Focus and Spot Size
The size and focus of the laser beam directly influence the level of detail and precision achievable in the engraving. A smaller spot size and tighter focus result in finer lines and intricate details, while a larger spot size may be suitable for faster but less detailed engraving. The laser beam’s proper focus ensures consistent engraving depth and sharpness across the entire design.
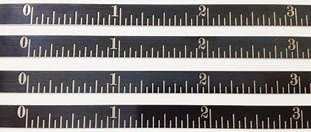
Engraving Speed and Power Density
Higher speeds may be preferred for larger areas or simpler designs to increase productivity. This efficiency is particularly beneficial for bulk engraving projects where time is critical. Conversely, slower speeds give the operator more precise control over the process, allowing fine lines to be accurately reproduced.

Engraving Depth and Resolution
Deeper engraving requires higher laser power and longer exposure times, while finer resolution demands tighter focus and slower engraving speeds. Balancing these factors ensures that the engraved markings meet the required depth, clarity, and quality specifications. It also enables the machine to achieve optimal efficiency and productivity while minimizing material waste and production costs.
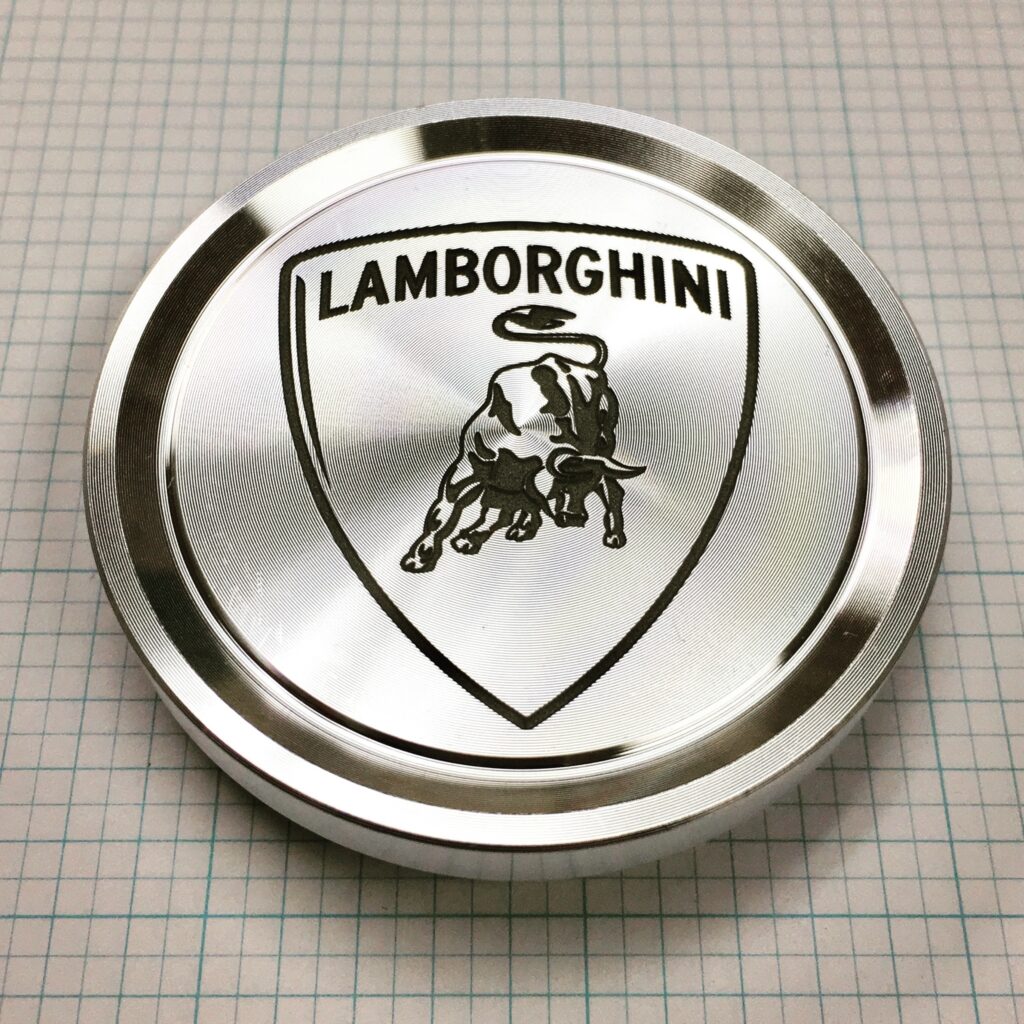
Operator Skill and Experience
Operator skill and experience are essential because a laser metal engraving machine can be challenging to operate efficiently and effectively. While the machine has sophisticated features, mastering its operation requires knowing the complexities of material interactions and equipment settings. Novice operators may find challenges in adjusting settings for different metals or reaching desired engraving depths.
Trends and Innovations in Laser Metal Engraving Technology
Here are some notable developments that are shaping the future of laser metal engraving machine technology:
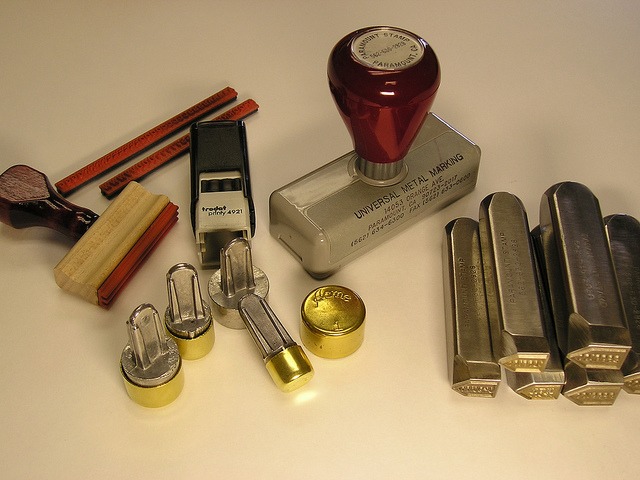
Portable and Compact Solutions
Miniaturization and portability drive the development of compact laser metal engraving systems suitable for on-site, in-field, or mobile applications. These solutions offer flexibility, convenience, and accessibility for small-scale manufacturing, customization, and personalization tasks in diverse industries, including jewelry, automotive, and electronics.

Green Laser Technology
Green laser sources are gaining traction for metal engraving applications due to their superior absorption characteristics and reduced thermal effects than infrared lasers. They offer better processing capabilities on reflective materials, thin films, and transparent substrates, enabling finer details, higher contrast, and improved surface quality.

Integration of AI and Machine Learning
Artificial intelligence (AI) and machine learning algorithms are being incorporated into laser engraving systems to automate process optimization, predictive maintenance, and quality control. These intelligent systems use sensors, cameras, and machine records data to detect trends, predict probable problems, and optimize engraving parameters.
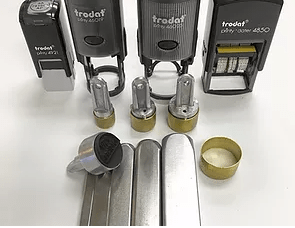
Multi-Axis Engraving Systems
Multi-axis laser metal engraving machines offer increased flexibility and precision by enabling engraving on complex three-dimensional surfaces and contours. These systems incorporate rotary axes and tilting mechanisms, allowing for engraving on curved, irregular, or non-flat objects with minimal setup time. They also support advanced techniques such as 3D relief engraving and texture mapping.
Choose Universal Metal Marking Co. for Your Part Marking Needs
Universal Metal Marking Co. takes pride in being a one-stop shop for all of your part marking needs! With over 30 services accessible, our industry knowledge and skills are unparalleled. We can meet and surpass your expectations, whether you need laser engraving, dot peen marking, chemical etching, impression stamping, or any other technique.